Typical Specifications of Shurjoint Mechanical Piping Methods
Note: This typical specification was written in accordance with CSI MasterFormat ’04, wherever applicable, where old division numbers 15 & 16 were superseded by new division numbers 20 through 29. The Division 21 covers Fire Suppression, Division 22 Plumbing and Division 23 HVAC.
Section 1: Basic Mechanical Methods and Materials (CSI 23 05 500):
1.1 System Description: Mechanical piping methods as manufactured or supplied by Shurjoint Piping Products are classified into four groups; the grooved piping method, shouldered piping method, plain-end piping method and hole-cut piping method. In all those methods, a mechanical coupling works as a connector between pipe and pipe, pipe and fitting, or fitting and fitting, sealed with a rubber gasket, and secured with bolts and nuts. These methods can be selected in lieu of the threaded, flanged, or welded method at buyer’s option. Shurjoint mechanical piping methods may be used in, but not limited to, the following piping systems subject to local code approval and installation in accordance with manufacturer’s installation instructions.
1.1.1 Plumbing (CSI Div. 22 00 00): Domestic hot & cold water, roof & storm drains, sanitary waste & vent
1.1.2 Heating & Air Conditioning (CSI Div. 23 00 00): Chilled water, condenser water, cooling water, machinery rooms, hot water heating, dual temperature water, utility water, Glycol, brine water
1.1.3 Fire Protection (CSI Div. 21 00 00): Wet & dry fire sprinklers, wet & dry standpipe, special hazards, Halon, FM200
1.1.4 Other Industrial Services: Mining, oilfield & power plant services, compressed air, process service water, elevator & lubricated oil systems, deionized water, vacuum service, chemical service, reverse osmosis, etc.
1.2 Design Pressure Ratings: Grooved products, shouldered products and hole-cut products shall have a minimum 300 psi (2.0 MPa) working pressure with a safety factor greater than 3 and shall be tested in accordance with ASTM F1476 and F1548 unless otherwise specified. Plain-end products shall have a minimum 150 psi (1.0 MPa) working pressure. Flange adapters shall be designed and tested in accordance with ANSI B16.5. Fire protection products shall be UL/ULC listed and FM approved with a minimum 175 psi (12 MPa) working pressure in accordance with NFPA 13. The rated working pressures shall be CWP, non-shock cold water pressure.
1.3 Service Temperatures: Mechanical piping products shall be used in the temperature range allowed for the rubber gasket used within the coupling.
1.4 Materials:
1.4.1 Pipe materials shall be carbon steel, stainless steel, copper tubing, ductile iron, HDPE, PVC, and CPVC. Carbon steel pipe shall be black or galvanized conforming to ASTM A53, A135, A795, or API 5L with OD tolerances as specified in AWWA C606 and Shurjoint published literature. For larger pipe sizes than 14” (DN350) or for high pressure services, OD of pipe shall be within the tolerances as specified in API 5L Table 8. Stainless steel pipe shall conform to ASTM A312 with the most suitable grade or type for the intended service. Copper tubing shall conform to ASTM B88 Type K, L, or M or ASTM B306 Type DWV. AWWA ductile iron pipe shall conform to AWWA C151/A21.51. HDPE (high density polyethylene) pipe shall conform to ASTM D2447, D3035 or F714 or shall conform to ISO 161/1, AS 1159 and DIN 8074, with wall thickness from SDR 32.5 to 7.3. CPVC pipe shall conform to ASTM F441, Sch.80 and F442 IPS SDR 13.5. PVC pipe shall conform to ASTM D1785.
1.4.2 Couplings, grooved-end fittings, flange adapters, mechanical-tees, valves and other system components shall be made of ductile iron, stainless steel casting or copper alloys. Ductile iron shall conform to ASTM A536 Gr. 65-45-12. Stainless steel casting shall conform to A351, Grade CF8 (Type 304) or Grade CF8M (Type 316). For elevated corrosive applications, other grades of stainless steel conforming to ASTM A351, 743, or 744 shall be selected. Copper alloys shall be lead-free bronze conforming to ASTM B584 C90500 (88-10-0-2) or C89836 (Bismuth bronze) or wrought copper conforming to ASTM B75 C12200.
1.4.3 Bolts and nuts shall be carbon steel heat-treated track bolts or stainless steel track bolts. Carbon steel track bolts shall conform to ASTM A183 Gr. B, minimum tensile strength 110,000 psi (758 MPa). Carbon steel hexagonal nuts shall conform to ASTM A563 Gr. A. Bolts and nuts shall be zinc electroplated to ASTM B633. Stainless steel track bolts shall conform to ASTM A193, Type 304 or Type 316, coated with molybdenum disulfide (MoS2) with stainless steel heavy duty nuts conforming to ASTM A194. As an option, silicon bronze nuts may be used with stainless steel bolts to avoid galling.
1.4.4 Gaskets shall be pressure responsive design, molded of Grade “E” EPDM or Grade “T” Nitrile elastomer as designated in ASTM D2000. The Grade “E” EPDM gasket shall be used for cold and hot water services for temperatures from -30oF (-34oC) to +230oF (+110oC), plus a variety of dilute acids, oil free air and other chemical services as allowed in the manufacturer’s gasket selection guide. The Grade “E” gasket shall not be used for petroleum oils, mineral oils, solvents, aromatic hydrocarbons and steam services. The Grade “T” Nitrile gasket shall be used in a variety of oil services including petroleum products*, vegetable oils, mineral oils, and air with oil vapors for temperatures from -20°F (-29°C) to +180°F (+82°C) and water for temperatures lower than +150°F (+65 °C). For other services, select the correct gasket grade in accordance with the manufacturer’s gasket selection guide. (* Not recommended for services of gasoline, diesel oil, jet fuels and or naphtha.
1.5 Pipe End Preparation:
1.5.1 Grooved Ends: Pipe ends of IPS carbon and stainless steel pipe and AWWA ductile iron pipe shall be roll-grooved or cut-grooved to AWWA C606. Pipe ends of ISO 4200 pipe, which superseded BS1387, DIN 2440 and DIN 2448 pipes, shall be roll-grooved or cut-grooved to ISO/FDIS 6182-12. For other special cut-grooves, refer to the manufacturer’s groove specifications. Pipe ends shall be clean and free from indentations, projections, burrs, rust or roll marks in the sealing area. To achieve optimum joint performance, roll grooves shall be well defined with vertical flanks. Standard wall pipe or Sch. 40 pipe smaller than 10” size shall be either roll-grooved or cut-grooved. Lightwall pipe, or unthreadable pipe, shall always be roll-grooved.
1.5.2 Shouldered Ends: Select Type “A” or “O” rings depending on the type of the coupling and weld rings according to the manufacturer’s installation instructions. Type “O” rings shall always be supplied from the coupling manufacturer.
1.5.3 Plain-Ends: Carbon steel and stainless steel pipes can be used as they are without any end preparation but pipes shall be softer than HB 150. HDPE (high density polyethylene) pipes can be used as they are without any end preparation. No plain-end couplings shall be used on other plastic pipe including PVC or CPVC.
1.5.4 Hole-Cutting: A hole shall be cut on the centerline of the pipe using the correct size hole saw as specified in the manufacturer’s hole-cutting specifications or installation instructions. Never use a torch for cutting a hole. All rough edges and burrs shall be removed and the area within 5/8” (16 mm) of the hole shall be smooth and free from dirt, scale or any imperfections.
1.5.5 Threaded-Ends: Pipes shall be threaded to ANSI B1.20.1 (NPT) or ISO 7 (BSPT) depending on the country or job where fittings are installed.
1.6 Assembly:
1.6.1 Couplings, fittings, flange adapters, valves and other system components shall be assembled in accordance with the manufacturer’s installation instructions.
1.6.2 Pipe ends and area around the hole shall be free from indentations, projections, burrs, roll marks, etc. in the area where gaskets are seated.
1.6.3 Gaskets shall be the proper style and grade suitable for the intended service. Refer to the manufacturer’s literature or installation instructions.
1.6.4 Lubrication: For general piping services, a thin layer of Shurjoint lubricant shall be applied to the entire exterior surface of the gasket including the gasket lips to avoid the gasket from pinching. For dry pipe and freezer systems, always use a petroleum-free silicone based lubricant. Do not use the Shurjoint standard lubricant for dry pipe and freezer systems.
1.7 Submittals (CSI 01 30 00)
1.7.1 Data sheets shall be submitted by the manufacturer on each product including installation instructions.
1.7.2 Product certificates shall be furnished only as required by the purchaser certifying the compliance of the products with the specifications and characteristics agreed upon between the purchaser and manufacturer.
1.8 Quality Assurance: The manufacturer shall be registered to ISO 9001: 2008 and a copy the certificate shall be available upon request.
1.9 Storage & Handling: The products shall be stored in manufacturer’s unopened packaging conditions until ready for installation. Environmental conditions (temperature, humidity, and ventilation) shall be maintained within the limits recommended by the manufacturer. Do not install products under environmental conditions outside manufacturer’s absolute limits.
Section 2: Hangers & Supports (CSI 21 05 29, 22 05 29 & 23 05 29)
2.1 Hangers & Supports: Hangers and supports on straight runs shall be applied in compliance with the requirements of local code, ANSI B31.1 Power Piping Code, B31.9 Building Services Piping Code, NFPA 13 Sprinkler Systems, or Mechanical Equipment Construction Guide (Japan) depending on the service intended and area where the system is installed. When Shurjoint flexible couplings are used on straight runs, location of hangers shall be designed as close to each coupling as possible, or within a distance of less than 1/6 the span.
Suggested Max. Span between Supports (steel pipe)
|
Nominal
Pipe Size
(in/mm)
|
Water Service (feet/meters)
|
Gas or Air Service(feet/meters)
|
1)
|
2)
|
3)
|
4)
|
1)
|
2)
|
3)
|
1 / 25
|
7 / 2.1
|
9 / 2.7
|
12 / 3.7
|
6.6 / 2.0
|
9 / 2.7
|
9 / 2.7
|
9 / 2.7
|
1.25 / 32
|
7 / 2.1
|
11 / 3.4
|
12 / 3.7
|
6.6 / 2.0
|
9 / 2.7
|
9 / 2.7
|
11 / 3.4
|
1.5 / 40
|
7 / 2.1
|
12 / 3.7
|
15 / 4.6
|
6.6 / 2.0
|
9 / 2.7
|
9 / 2.7
|
13 / 4.0
|
2 / 50
|
10 / 3.1
|
13 / 4.0
|
15 / 4.6
|
6.6 / 2.0
|
13 / 4.0
|
13 / 4.0
|
15 / 4.6
|
3 / 80
|
12 / 3.7
|
15 / 4.6
|
15 / 4.6
|
6.6 / 2.0
|
15 / 4.6
|
15 / 4.6
|
17 / 5.2
|
4 / 100
|
14 / 4.3
|
17 / 5.2
|
15 / 4.6
|
6.6 / 2.0
|
17 / 5.2
|
17 / 5.2
|
21 / 6.4
|
6 / 150
|
17 / 5.2
|
20 / 6.1
|
15 / 4.6
|
10 / 3.0
|
21 / 6.4
|
21 / 6.4
|
25 / 7.6
|
8 / 200
|
19 / 5.8
|
21 / 6.4
|
15 / 4.6
|
10 / 3.0
|
24 / 7.3
|
24 / 7.3
|
28 / 8.5
|
10 / 250
|
19 / 5.8
|
21 / 6.4
|
|
10 / 3.0
|
24 / 7.3
|
24 / 7.3
|
31 / 9.5
|
12 / 300
|
23 / 7.0
|
21 / 6.4
|
|
10 / 3.0
|
30 / 9.1
|
30 / 9.1
|
33 / 10.1
|
14 / 350
|
23 / 7.0
|
21 / 6.4
|
|
|
30 / 9.1
|
30 / 9.1
|
33 / 10.1
|
16 /400
|
27 / 8.2
|
21 / 6.4
|
|
|
35 / 10.7
|
35 / 10.7
|
33 / 10.1
|
18 /450
|
27 / 8.2
|
21 / 6.4
|
|
|
35 / 10.7
|
35 / 10.7
|
33 / 10.1
|
20 /500
|
30 / 9.1
|
21 / 6.4
|
|
|
39 / 11.9
|
39 / 11.9
|
33 / 10.1
|
24 / 600
|
32 / 9.8
|
21 / 6.4
|
|
|
42 / 12.8
|
42 / 12.8
|
33 / 10.1
|
1) ANSI B31.1 Power Piping Code
2) ANSI B31.9 Building Services Piping Code
3) NFPA 13 Sprinkler systems
4) Ministry of Land & Transportation of Japan: Mechanical Equipment Construction Guide
Section 3: Mechanical Piping Methods for Plumbing (CSI Div. 22 00 00), HVAC (CSI Div. 23 00 00) & Other Industrial Services
3.1 General: Shurjoint mechanical piping methods (grooved piping method, shouldered piping method, plain-end piping method and hole-cut piping method) are acceptable for use on domestic water systems, storm drains, roof drains or vent piping systems under service temperatures less than 230°F (110°C), cooling systems, chilled water piping, including risers mains, equipment connection, branches, supply and return lines, cooling tower piping, dual temperature systems piping or condenser water piping within the temperature range of -30oF (-34oC) to +230oF (+110oC), or on hot water systems including boiler manifolds, mains, risers, branches, supply and return lines under operating conditions not exceeding +230oF (+110oC) subject to local code approval and installation in accordance with manufacturer’s installation instructions. Thermal stress shall be calculated based on the manufacturer’s published literature to determine whether the system will accommodate such movement or whether to add expansion joints or other movement compensators.
3.2 Couplings: Couplings shall be made of ductile iron conforming to ASTM A536 Gr. 65-45-12 with bolts and nuts conforming to ASTM A183 Gr. B and A563 Gr. A respectively. Standard Grade “E” gaskets shall be used for all water systems. For other service fluids, select the correct gasket grade and type in accordance with the manufacturer’s gasket selection guide.
3.2.1 Rigid grooved couplings shall be Shurjoint Model Z07 for regular or moderate pressure services on 1¼” (DN32) through 24” (DN600) sizes. For high pressure services, rigid grooved couplings shall be Shurjoint Model XH-1000 (up to 1000 psi or 6.9 MPa) with standard gasket or XH-70EP (up to 2,500 psi or 17.5 MPa) with EP gasket for pipe sizes 2” (DN50) through 12” (DN300). For Model XH-70EP, pipe end shall be always cut-grooved to the manufacturer’s EP cut-groove specification.
3.2.2 Flexible grooved couplings shall be Shurjoint Model 7705 (moderate pressure) for sizes 1” (DN25) through 12” (DN300) or Model 7707 (higher pressure) for sizes ¾” (DN20) through 12” (DN300) where system flexibility is required or desired. For sizes 14” (DN350) through 26” (DN650), use Model 7707N flexible grooved couplings. For roll-grooved pipe larger than 28” (DN700) up to 42” (DN1050), use Model 7707L* grooved couplings. (*Model 7707L is not classified as a flexible coupling due to limited angular deflection).
3.2.3 Outlet mechanical couplings shall be Shurjoint Model C-7, which shall provide a reducing branch outlet without the use of a tee, mechanical tee, or the welding method, for sizes 1½" x 1/2” (DN40 x DN15) through 6" x 2” (DN150 x DN50).
3.2.4 Reducing grooved couplings shall be Shurjoint Model 7706, which shall provide a direct reduction of run pipe sizes 1½” x 1¼” (DN40 x DN32) through 8” x 6” (DN200 x DN150).
3.2.5 Transition couplings from IPS pipe sizes to JIS pipe sizes shall be Shurjoint Model 7771-T for pipe sizes 8” (DN200) through 12” (DN300).
3.2.6 Hinged lever couplings (or toggle coupling) shall be Shurjoint Model G-28, which shall be used for frequent connect and disconnect services, for size 1½” (DN40) through 12” (DN300). The coupling shall have a safety device to prevent accidental opening of the coupling.
3.2.7 Ring-joint couplings (or shouldered coupling for use with Type “O” rings) shall be Shurjoint Model R-88 for sizes 8” (DN200) through 96” (DN2400) (moderate pressure) or Model R-88N for sizes 14” (DN350) through 24” (DN600) (moderate pressure, two segment type). For higher pressure services, use Shurjoint Model RH-1000 (1000 psi) for pipe sizes 8” (DN200) through 12” (DN300), RX-3000 (3000 psi) for 4” (DN100) through 12” (DN300), or RX-3770 (3770 psi) for 8” (DN200) through 12” (DN300). A pair of steel rings (Type “O” shoulder rings) shall be supplied from the coupling manufacturer and shall be installed in accordance with the manufacturer’s installation instructions.
3.2.8 Shouldered couplings (for use with Type “A” shoulder rings) shall be Shurjoint Model S35 for sizes 2” (DN50) through 8” (DN200) or Model SD-28 toggle type shouldered coupling for frequent connect and disconnect services for sizes 3” (DN80) through 6” (DN150). Shouldered couplings Model S35 and SD-28 shall be supplied in hot-dip galvanized finish with a Grade T Nitrile gasket.
3.3 Flange Adapters for direct connection from an ANSI Class 125 / Class 150 (or PN 10 / PN 16) flanged system to a grooved system shall be Shurjoint Model 7041 for sizes 2” (DN50) through 12” (DN300) and or Model 7041N (two-segment type) for sizes 14” (DN350) through 24” (DN600). For ANSI Class 300 systems, use Shurjoint Model 7043 flange adapters for sizes 2” (DN50) through 12” (DN300). Flange adapters shall be supplied with Grade “E” EPDM gasket and one or a pair of hexagonal bolts for joining the flange segments. Drillings shall conform to and testing shall be conducted in accordance with ANSI B16.5 Class 150 or Class 300 requirements. Flange adapters shall be hinged as a single unit for sizes 2” (DN50) through 12” (DN300) and shall be supplied with a drawer kit for sizes larger than 14” (DN350).
3.4 Solid Flange Adapters shall be Shurjoint Model 7170 flange adapters or Model 7180 universal flange adapters for pipe sizes 2” (DN50) through 8” (DN200). Use Shurjoint Model 7181 universal flange adapters for direct reduction of run pipe for sizes 3” x 2” (DN80 x DN50) through 6” x 4” (DN150 x DN100). Drillings of Model 7170 shall conform to ANSI B16.5 Class 150 (or PN 10 / PN 16). Drillings of Model 7180 and 7181 shall fit ANSI Class 125, Class 150, PN 10, PN 16, BS-10E, and JIS 10K flanges. Testing shall be conducted in accordance with ANSI B16.5 Class 150 requirements.
3.5 Mechanical Tees shall be Shurjoint mechanical tees Model 7721 (threaded outlet) or Model 7722 (grooved outlet), which shall provide a mid-point branch outlet without the use of multiple fittings or the welding method. Available sizes shall be from 2” x ½” (DN50 x DN15) through 8” x 6” (DN200 x DN150). A hole shall be cut or drilled before the mechanical tee is installed in accordance with the manufacturer’s installation instructions. Mechanical tees shall be supplied with a Grade “E” EPDM gasket a pair of bolts and nuts.
3.6 Grooved-end Fittings shall be Shurjoint Models 7110 (90° Elbow), 7111 (45° Elbow), 7112 (22½° Elbow). 7113 (11¼° Elbow), 7120 (Tee), 7130 (45° Lateral), 7135 (Cross), 7121 (Reducing Tee), 7150 (Concentric Reducer), 7151 (Eccentric Reducer), 7110LR (1.5D 90° Elbow), 7111LR (1.5D 45° Elbow), 7137 (True-Y), 7118 (90° Adapter Elbow), 7119 (45° Adapter Elbow), 7110-B (90° Elbow with Base Support), and 7160 & 7160H (End Cap) for sizes 1” (DN25) through 24” (DN600). Grooves shall conform to AWWA C606 and or Shurjoint groove specifications. C-to-E dimensions of ductile iron made grooved-end fittings shall conform to the manufacturer’s standard. C-to-E dimensions of wrought steel fabricated grooved-end fittings shall conform to ANSI B16.9 or custom-made to the purchase order. For higher pressure services, use Shurjoint Models 10EP (90° Elbow), 11EP (45° Elbow), 20EP (Tee), 35EP (Cross), or 22EP (Header Tee) or custom-made fabricated fittings.
3.7 Welding Outlet Fittings shall be Shurjoint Model 71 (female threaded), Model 72R (roll grooved), or Model 72C (cut grooved), which shall provide a mid-point branch outlet by welding. Female threaded outlet fittings shall be made of weldable carbon steel conforming to SAE J403 and outlet sizes shall be available ½” (DN20) through 4” (DN100) on pipe runs 1¼” (DN32) through 8” (DN200). Roll-grooved outlet fittings shall be made from Sch. 10 steel pipe and outlet sizes shall be available 1¼” (DN32) through 4” (DN100). Cut-grooved outlet fittings shall be made from Sch. 40 steel pipe for outlet sizes 2” (DN50) to 8” (DN200). The rated working pressure shall be 300 psi (2.0 MPa).
3.8 Threaded Fittings shall be Shurjoint series 800 ductile iron threaded fittings, rated 300 psi, made of ductile iron castings conforming to ASTM A536 Gr. 65-45-12 with dimensions conforming to ANSI B16.3* Class 150 and threads to ANSI B1.20.1 NPT. Standard Shurjoint threaded fittings are provided with a black (bare metal) finish with thin rust-proof oil, or hot dip galvanized or electro-zinc plated. (*Dimensions of Shurjoint Model 827 Bushings and Model 819 Plugs to ANSI B16.14, 830 Unions to ANSI 16.39 Class 150 & Model 841 Companion Flanges to B16.42 Class 150.)
3.9 Swing Check Valves:
3.9.1 Grooved-end swing check valves shall be Shurjoint Model SJ-900, 2½” (DN65) through 12” (DN300), consisting of ductile iron valve body, spring-loaded clapper and non-stick Grade “E” EPDM or Grade “T” Nitrile rubber sheet. The rated working pressure shall be 300 psi.
3.9.2 Grooved-end dual disc check valves shall be Shurjoint Model SJ-915, 2½” (DN65) through 24” (DN600), consisting of ductile iron valve body with a Grade “T” Nitrile or Grade “E” EPDM seat molded to the body and dual 304 stainless steel disc. The rated working pressure shall be 300 psi up to 12” (DN300) and 240 psi over 14” (DN350).
3.10 Butterfly Valves:
3.10.1 Grooved-end butterfly valves shall be Shurjoint Model SJ-300N, rated 300 psi, 2” (DN50) through 24” (DN600), consisting of a ductile iron body to ASTM A536 Gr. 65-45-12, epoxy powder coated, with ductile iron disc encapsulated with Grade “E” EPDM or Grade “T” Nitrile elastomer and stainless steel stems. Valves shall be equipped with a 10-position lever handle (SJ-300N-L) or worm gear operator (SJ-300N-W). Face-to-face dimensions shall conform to MSS SP-67.
3.10.2 Low-profile butterfly valves shall be Shurjoint Model SJ-200, rated 200 psi, 2” (DN50) through 8” (DN200), consisting of a ductile iron body to ASTM A536 Gr. 65-45-12 with Grade “T” Nitrile rubber lining, CF8M (Type 316) stainless steel disc and Type 416 stainless steel stems. Valves shall be equipped with a tamper resistant locking device. Face-to-face dimensions shall conform to MSS SP-67.
3.11 Grooved-end Ball Valves shall be Shurjoint Model SJ-500, standard port, rated 1000 psi for sizes 1½” DN(40) through 3” (DN80), 800 psi for 4” (DN100) and 600 psi for 6” (DN150), consisting of ductile iron body to ASTM A536 Gr. 65-45-12, Type 304 stainless steel trim, and virgin TFE seats, equipped with a lever handle with a tamper resistant locking device (SJ-500L), or worm gear operator (SJ-500W).
3.12 Strainers:
3.12.1 Grooved-end T-type strainers shall be Shurjoint Model 728, rated 300 psi, 2” (DN50) through 14” (DN350), consisting of body, cap, and Model Z07 coupling, made of ductile iron casting to ASTM A536 Gr. 65-45-12, and Type 304 stainless steel mesh screen.
3.12.2 Grooved-end Y-type strainers shall be Shurjoint Model 726, 2” (DN50) through 16” (DN400), rated 300 psi up to 6” (DN150) and 175 psi over 8” (DN200), consisting of body, cap, and Model Z07 coupling, made of ductile iron casting to ASTM A536 Gr. 65-45-12, and a Type 304 stainless steel perforated screen.
3.13 Grooved-end Suction Diffusers shall be Shurjoint Model 725, rated 300 psi, with grooved x grooved ends (725G) or grooved x flanged ends (725F), 2½” x 2½” (DN65 x DN65) through 20” x 14” (DN500 x DN350). Bodies shall be made of ductile iron conforming to ASTM A536 Gr. 65-45-12, or fabricated from carbon steel pipe to A53 or equal depending on diffuser size. Flanged ends shall be drilled to ANSI B16.5 Class 150. Suction diffusers shall be supplied with a perforated Type 304 stainless steel strainer and a disposable fine mesh screen to protect the pump during start-up operation.
3.14 Grooved-end Expansion Joints shall be Shurjoint Model 650N, rated 300 psi, 2” (DN50) through 6” (DN150), or Model 651, rated 300 psi, 1½” (DN40) through 8” (DN200). Both expansion joints shall consist of a number of grooved couplings and carbon steel pipe sleeves sealed with Grade “E” EPDM gaskets. Proper supports shall be applied to the expansion joint in accordance with the manufacturer’s installation instructions.
Section 4: Grooved Fire Protection Systems (CSI Div. 21 00 00)
4.1 General: Shurjoint grooved products listed by UL/ULC and or approved by FM are acceptable for use on wet and dry automatic sprinklers, inspector drain lines, outside protection, low pressure carbon dioxide, FM-200, Halon and Halon replacement systems subject to local code approval and installation in accordance with manufacturer’s installation instructions. Products shall be installed in accordance with the latest version of NFPA 13 standards, local Fire Marshall Code and latest published Shurjoint installation instructions. Shurjoint products are applicable for above or under ground fire protection systems. For special hazard systems, consult a Shurjoint representative.
4.2 Pipe: Pipe shall be carbon steel pipe, standard wall or lightwall, conforming to ASTM A53, A135, A795 or other UL listed/FM approved pipe.
4.2.1 Pipe End Preparation: Pipe ends shall be roll-grooved or cut-grooved in accordance with AWWA C606 or Shurjoint groove specifications. Pipe ends shall be free from indentations, projections, burrs, roll marks, etc. in the area where gaskets are seated.
4.2.1 Hole-Cutting: A hole shall be cut on the centerline of the pipe using the correct size hole saw as specified in the manufacturer’s hole-cutting specifications or installation instructions. Never use a torch for cutting a hole. All rough edges and burrs shall be removed and the area within ⅝” (16 mm) of the hole shall be smooth and free from dirt, scale or any imperfections.
4.3 Couplings: Couplings shall be made of ductile iron conforming to ASTM A536 Gr. 65-45-12 with bolts and nuts conforming to ASTM A183 Gr. B and A563 Gr. A respectively. Standard Grade “E” gaskets shall be used for wet automatic sprinkler systems. The Shurjoint GapSeal® gaskets shall be used for dry pipe fire protection systems and freezer applications. For dry systems under 0°F (-18°C), Grade “L” Silicone gaskets shall be used.
4.3.1 Rigid grooved couplings shall be Shurjoint Model Z05, rated 300 psi, 1¼” (DN32) through 8” (DN200).
4.3.2 Flexible grooved couplings shall be Shurjoint Model 7705, rated 300 psi, 1” (DN25) through 12” (DN300).
4.3.3 Reducing grooved coupling shall be Shurjoint Model 7706, which shall provide direct reduction of pipe runs 1½” x 1¼” (DN40 x DN32) through 8” x 6” (DN200 x DN150).
4.3.4 Outlet mechanical couplings shall be Shurjoint Model C-7 outlet coupling, which shall provide a reducing branch outlet without the use of a tee, mechanical tee, or welding, for sizes 1½" x ½” (DN40 x DN15) through 6" x 2” (DN150 x DN50).
4.4 Flange Adapters for direct connection: Flange adapters for direct connection from an ANSI Class 125 / Class 150 (or PN 10 / PN 16) flanged system to a grooved system shall be Shurjoint Model 7041 for sizes 2” (DN50) through 12” (DN300). Flange adapters shall be supplied with a Grade “E” EPDM gasket and a hexagonal bolt for joining the flange segments. Drillings shall conform to and testing shall be conducted in accordance with ANSI B16.5 Class 150. Flange adapters shall be hinged as a single unit.
4.5 Solid Flange Adapters shall be Shurjoint Model 7170 flange adapters or Model 7180 universal flange adapters for pipe sizes 2” (DN50) through 8” (DN200). Use Shurjoint Model 7181 universal flange adapters for direct reduction of run pipe for sizes 3” x 2” (DN80 x DN50) through 6” x 4” (DN150 x DN100). Drillings of Model 7170 shall conform to ANSI B16.5 Class 150 (or PN 10 / PN 16). Drillings of Model 7180 and 7181 shall fit ANSI Class 125, Class 150, PN 10, PN 16, BS-10E, and JIS 10K flanges. Testing shall be conducted in accordance with ANSI B16.5 Class 150 requirements.
4.6 Mechanical Tees shall be Shurjoint Model M21 (threaded outlet) or Model M22 (grooved outlet), which shall
provide a mid-point branch outlet without the use of multiple fittings or welding. Available sizes shall be from 2” x ½” (DN50 x DN15) through 8” x 6” (DN200 x DN150). For direct connection of a sprinkler head, use Shurjoint Model 723 mechanical tees, 1¼” (DN32) x ½” (DN15) through 2½” (DN65) x 1” (DN25). A hole shall be cut or drilled before the mechanical tee is installed in accordance with the manufacturer’s installation instructions. Mechanical tees shall be supplied with a Grade “E” EPDM gasket and a pair of bolts and nuts.
4.7 Grooved-end Fittings: Grooved-end fittings shall be Shurjoint Models 901 (90° Elbow – short radius), 903 (Tee – short radius), 7110 (90° Elbow), 7111 (45° Elbow), 7112 (22½° Elbow). 7113 (11¼° Elbow), 7120 (Tee), 7130 (45° Lateral), 7135 (Cross), 7121 (Reducing Tee), 7150 (Concentric Reducer), 7151 (Eccentric Reducer), 7110DR (Drain Elbow), 7127 (Standpipe Tee), 7125 (Bullhead Tee, 7150F & M (Reducing Socket & Nipple), 55 (Nipple Adapter, 7114 (Hydrant Elbow), 7122 (Hydrant Tee), 7133 (Pitcher Tee), 850/851/853 (Sprinkler Hubs), 899 (End-All Fitting), and 7160 (End Cap). Size ranges shall be 1” (DN25) through 12” (DN300). Grooved-end fittings shall be made of ductile iron conforming to ASTM A536 Gr. 65-45-12 with grooved ends to AWWA C606 or Shurjoint groove specifications.
4.8 Welding Outlet Fittings shall be Shurjoint Model 71 (female threaded), Model 72R (roll grooved), or Model 72C (cut grooved), which shall provide a mid-point branch outlet by welding. Female threaded outlet fittings shall be made of weldable carbon steel conforming to SAE J403 and outlet sizes shall be available ½” (DN20) through 4” (DN100) on pipe runs 1¼” (DN32) through 8” (DN200). Roll-grooved outlet fittings shall be made from Sch. 10 steel pipe and outlet sizes shall be available 1¼” (DN32) through 4” (DN100). Cut-grooved outlet fittings shall be made from Sch. 40 steel pipe for outlet sizes 2” (DN50) to 8” (DN200). The rated working pressure shall be 300 psi (2.0 MPa).
4.9 Threaded Fittings shall be Shurjoint series 800 ductile iron threaded fittings, rated 300 psi, made of ductile iron castings conforming to ASTM A536 Gr. 65-45-12 with dimensions conforming to ANSI B16.3* Class 150 and threads to ANSI B1.20.1 NPT. Standard Shurjoint threaded fittings are provided with a black (bare metal) finish with thin rust-proof oil, or hot dip galvanized or electro-zinc plated. (*Dimensions of Shurjoint Model 827 Bushings and Model 819 Plugs to ANSI B16.14, 830 Unions to ANSI 16.39 Class 150 & Model 841 Companion Flanges to B16.42 Class 150.)
4.10 Swing Check Valves: Grooved-end swing check valves shall be Shurjoint Model RCV, rated 300 psi, 2½” (DN65) through 8” (DN200), consisting of ductile iron valve body conforming to ASTM A536 Gr. 65-45-12, spring-loaded clapper and non-stick Grade “E” EPDM rubber sheet.
4.11 Butterfly Valves: Grooved-end butterfly valves shall be Shurjoint Model SJ-700W, rated 175 psi, 2½” (DN65) through 8” (DN200), consisting of a ductile iron valve body conforming to ASTM A536 Gr. 65-45-12, Nylon coated, and Grade “E” EPDM encapsulated disc. The butterfly valves shall be equipped with a worm gear operator with wiring.
Section 5: Stainless Steel Grooved Piping Systems
5.1 General: Shurjoint grooved products are acceptable, at buyer’s option, for use with stainless steel pipe for a various applications including food industries, chemical plants, potable water supply, reverse osmosis desalination plants, etc. with service temperatures less than 230°F (110°C) subject to local code approval and installation in accordance with manufacturer’s installation instructions.
5.2 Pipe: Pipe shall be stainless steel conforming to ASTM A312 and an appropriate grade and wall thickness shall be selected for the intended service. Sch. 5S stainless steel pipe shall not be used with Shurjoint grooved couplings.
5.2.1 Pipe End Preparation: Pipe ends shall be roll-grooved or cut-grooved in accordance with AWWA C606 or Shurjoint groove specifications. Pipe ends shall be free from indentations, projections, burrs, roll marks, etc. in the area where gaskets are seated. To achieve optimum joint performance, roll grooves shall be well defined with fully formed vertical flanks.
5.2.2 Hole-Cutting: A hole shall be cut on the centerline of the pipe using the correct size hole saw as specified in the manufacturer’s hole-cutting specifications or installation instructions. Never use a torch for cutting a hole. All rough edges and burrs shall be removed and the area within ⅝” (16mm) of the hole shall be smooth and free from dirt, scale or any imperfections.
5.3 Couplings: Couplings shall be made of stainless steel castings conforming to ASTM A351 Grade CF8M (Type 316) or Grade CF8 (Type 304). Other grades including CD3MN (Duplex 2205), CE8MN, CE3MN (Duplex 2507), CD3McuN (254SMO) per ASTM A351, A743, or A744 are optional. As an option, Shurjoint ductile iron couplings can be used in conjunction with stainless steel pipe for services in a non-corrosive environment.
5.4 Bolts: Stainless steel track bolts shall conform to ASTM A193, Type 304 or Type 316, coated with molybdenum disulfide (MoS2) with stainless steel heavy duty nuts conforming to ASTM A194. As an option, silicon bronze nuts may be used with stainless steel bolts to avoid galling.
5.5 Gaskets: Gaskets shall be pressure responsive design, molded of Grade “E” EPDM or Grade “T” Nitrile elastomer as designated in ASTM D2000. The Grade “E” EPDM gasket shall be used for cold and hot water services for temperatures from -30oF (-34oC) to +230oF (+110oC), plus a variety of dilute acids, oil free air and other chemical services as allowed in the manufacturer’s gasket selection guide. The Grade “E” gasket shall not be used for petroleum oils, mineral oils, solvents, aromatic hydrocarbons and steam services. The Grade “T” Nitrile gasket shall be used in a variety of oil services including petroleum products*, vegetable oils, mineral oils, and air with oil vapors for temperatures from -20°F (-29°C) to +180°F (+82°C) and water for temperatures lower than +150°F (+65 °C). For other services, select the correct gasket grade in accordance with the manufacturer’s gasket selection guide. (* Not recommended for services of gasoline, diesel oil, jet fuels and or naphtha.
5.6 Grooved Couplings:
5.6.1 Rigid grooved couplings shall be Shurjoint Model SS-7, 1¼” (DN32) through 8” (DN200), rated 400 psi (2.8 MPa) for use with Sch. 40S or 10S roll or cut grooved pipe, and Model SS-7X, 10” (DN250) through 24” (DN600), rated 300 psi (2.0 MPa) for use with Sch. 40S or 10S roll or cut grooved pipe. Models SS-7 and SS-7X shall be made of CF8 (Type 304) or CF8M (Type 316) stainless steel per ASTM A351.
5.6.2 Flexible grooved couplings shall be Shurjoint Model SS-8, 1” (DN25) through 8” (DN200), rated 300 psi (2.0 MPa) for use with Sch. 40S or 10S roll or cut grooved pipe.
5.6.3 For high pressure services including reverse osmosis, desalination and other specialty systems, flexible grooved couplings shall be Shurjoint Model SS-1200 and Model SS-8X which shall be used only with cut-grooved Sch. 40S or thicker pipe. The Model SS-1200 shall be rated 1200 psi (8.3 MPa) for sizes ¾” (DN20) through 4” (DN100) and shall be made of CD3MN (Duplex 2205), CE8MN, CE3MN (Duplex 2507), CD3MCuN (254SMO) per ASTM A351, A743, or A744. The Model SS-8X shall be rated 1400 psi (9.7 MPa) for use with ¾” (DN20) through 8” (DN200) Sch. 40S cut grooved pipe and 1000 psi (6.9 MPa) for use with 5” (DN125) through 8” (DN200) Sch. 40S cut grooved pipe. The Model SS-8X couplings shall be made of CF8 (Type 304) or CF8M (Type 316) per ASTM A351.
5.7 Flange Adapters:
5.7.1 Flange adapters for direct connection from an ANSI Class 125 / Class 150 (or PN 10 / PN 16) flanged system to a grooved system shall be Shurjoint Model SS-41 flange adapters for sizes 2” (DN50) through 8” (IDN200). Model SS-41 flanges shall be made of CF8 (Type 304) or CF8M (Type 316) per ASTM A351. Flange adapters shall be supplied with a Grade “E” EPDM gasket and a pair of hexagonal bolts for joining the flange segments. Drillings shall conform to and testing shall be conducted in accordance with ANSI B16.5 Class 150 requirements.
5.7.2 Solid flange adapters shall be Shurjoint Model SS-80 universal flange adapters for sizes 2” (DN50) through 8” (DN200). Model SS-80 shall be made of CF8 (Type 304) or CF8M (Type 316) per ASTM A351. Drillings of Model SS-80 shall fit ANSI Class 125, Class 150, PN 10, PN 16, BS-10E, and JIS 10K flanges. Testing shall be conducted in accordance with ANSI B16.5 Class 150 requirements.
5.8 Grooved-end Fittings: Grooved-end fittings shall be Shurjoint Models SS-10 (90° Elbow), SS-11 (45° Elbow), SS-20 (Tee), SS-21 (Reducing Tee) & SS-50 (Concentric Reducer), SS-60 (End Cap). Grooved-end fittings shall be made of investment castings or wrought stainless steel, CF8 (Type 304) or CF8M (Type 316), with end preparation to AWWA C606. Other grades including CD3MN (Duplex 2205), CE8MN, CE3MN (Duplex 2507), CD3MCuN (254SMO) per ASTM A351, A743, or A744 are optional.
5.9 Butterfly Valves: Grooved-end butterfly valves shall be Shurjoint Model SJ-400L, rated 300 psi, 2” (DN50) through 8” (DN200), consisting of CF8M (Type 316) body per ASTM A351 with dual-seal rubber encapsulated disc. The rubber encapsulation shall be Gr. “E-pw” EPDM for cold and hot potable water use, UL Classified in accordance with ANSI/NSF61, or Grade “T” Nitrile for oil services. The valve shall be equipped with a 10-position lever handle.
5.10 Ball Valves: Grooved-end ball valves shall be Shurjoint Model SJ-600, 2” (DN50) through 4” (DN100), rated 600 psi, consisting of CF8M (Type 316) body, ball and stem. The valve shall be full port type in conformance with MSS SP110 and SP72 requirements. Grooved-end ball valves shall be equipped with a lever handle (SJ-600L) or with a worm gear operator (SJ-600W).
5.11 Strainers: Grooved-end Y-type strainers shall be Shurjoint Model SS-726, 2½” (DN65) through 6” (DBN150), rated 300 psi, consisting of consisting of a CF8 (Type 304) body and Type 304 perforated screen, assembled with a SS-7 coupling and SS-60 cap.
5.12 Mechanical Tees: For branch connection or direct connection to sprinkler heads, drop nipples and or gauges on stainless steel pipe, use Shurjoint Model SS-723 mechanical tees, 1¼” (DN32) x ½” (DN15) through 2” (DN50) x 1” (DN25), consisting of a CF8 (Type 304) stainless steel body per ASTM A351, Grade “E” EPDM gasket and Type 304 stainless steel track bolts and nuts.
Section 6: Copper Tubing Grooved Piping Systems
6.1 General: The Shurjoint grooved method can be selected for joining copper tubing in lieu of the solder joint method at buyer’s option and may be used in, but not limited to, plumbing, drains, waste and vents subject to local code approval and installation in accordance with manufacturer’s installation instructions.
6.2 Copper Tubing: Copper tubing shall conform to ASTM B88 Type K, L, or M and or ASTM B306 Type DWV.
6.2.1 Pipe End Preparation: Pipe ends shall be roll-grooved in accordance with Shurjoint grooving specifications. Pipe ends shall be free from indentations, projections, burrs, roll marks, etc. in the area where gaskets are seated. To achieve optimum joint performance, roll grooves shall be as defined as possible.
6.2.2 Hole-Cutting: A hole shall be cut on the centerline of the pipe using the correct size hole saw as specified in the manufacturer’s hole-cutting specifications or installation instructions. Never use a torch for cutting a hole. All rough edges and burrs shall be removed and the area within ⅝” (16 mm) of the hole shall be smooth and free from dirt, scale or any imperfections.
6.3 Couplings: Couplings shall be made of ductile iron conforming to ASTM A536 Gr. 65-45-12, epoxy coated.
6.4Bolts: Carbon steel track bolts shall conform to ASTM A183, minimum tensile strength 110,000 psi, zinc plated to ASTM B633 with carbon steel heavy duty nuts per ASTM A563 Gr. A.
6.5 Gaskets - Gaskets shall be a pressure responsive design, molded of Grade “E” EPDM or Grade “T” Nitrile elastomer as designated in ASTM D2000. The Grade “E” EPDM gasket shall be used for cold and hot water services for temperatures from -30oF(-34oC) to +230oF (+110oC), plus a variety of dilute acids, oil free air and many chemical services. Grade “E” gaskets are not recommended for petroleum oils, mineral oils, solvents, aromatic hydrocarbons and steam services. For other services, select the correct gasket grade in accordance with the manufacturer’s gasket selection guide.
6.6 Grooved Couplings:
6.6.1 Rigid grooved couplings shall be Shurjoint Model C305 for CTS (copper tubing) sizes 2” (DN50) through 8” (DN200). Housing segments shall be made of ductile iron per ASTM A536 Gr. 65-45-12, epoxy coated in bronze color, supplied with a Grade E EPDM GapSeal®* gasket. (*The GapSeal® gasket shall be designed to seal the gap between the pipe ends.)
6.6.2 Reducing grooved couplings shall be Shurjoint Model C306 for CTS (copper tubing) sizes 2½” x 2” (DN 65 x DN50) through 6” x 4” (DN150 x DN100), epoxy coated in bronze color with a Grade E EPDM gasket.
6.6.3 For transition from an IPS grooved system to a grooved end CTS (copper tubing) system, use Shurjoint Model C307 couplings for sizes 2” (DN50) through 4” (DN100). For transition from a grooved AWWA ductile iron pipe to a grooved end CTS (copper tubing) system, use Shurjoint Model C307-AC couplings for the size of AWWA DI pipe 4” (DN100) x CTS 3” (DN80).
6.7 Flange Adapters: Flange Adapters for direct connection from an ANSI Class 125 / Class 150 (or
ASME B16.24) flanged system to a grooved end CTS (copper tubing) shall be Shurjoint Model C341 for sizes 2” (DN50) through 6” (DN150). Model C341 flange adapters shall be made of ductile iron per ASTM A536 Gr. 65-45-12, epoxy coated in bronze color, with a Grade “E” EPDM gasket and a pair of hexagonal bolts for joining the flange segments. Drillings shall conform to and testing shall be conducted in accordance with ANSI B16.5 Class 150 requirements.
6.8 Grooved-end Fittings: Grooved-end fittings shall be Shurjoint Models C10 (90° Elbow), C11 (45° Elbow), C20
(Tee), C60 (Cap), C21 (Reducing Tee), C50 (Concentric Reducer), C26 (Reducing Tee – Gr x Gr x Cup), C52 (Concentric Reducer Gr x Cup), C55 (Transition Adapter – IPS female threaded x CTS grooved), and C55T (Transition Adapter with ¼” tap). Grooved-end fittings shall be made of lead-free bronze casting per ASTM B584 copper ally C90500 or C89360.
6.9 Bronze Mechanical Tees: Bronze mechanical tees shall be Shurjoint Model C723 for sizes 2½” x ¾” (DN65 x DN20) through 4” x 1¼” (DN100 x DN32). The upper housing segment shall be made of lead-free bronze alloy C90500 per ASTM B584, which shall be UL classified in accordance with ANSI/NSF61 for potable water use. The lower housing segment shall be ductile iron per ASTM A536 Gr. 65-45-12, epoxy coated in bronze color. The mechanical tee shall have a female threaded outlet, NPT per ANSI B1.20.1 or BSPT per ISO 7, supplied with an EPDM O-ring and carbon steel track bolts and nuts.
6.10 Butterfly Valves: Grooved-end butterfly valves for CTS (copper tubing) shall be Shurjoint Model SJ-C300, rated 300 psi, 2” (DN50) through 6” (DN150), consisting of a bronze body per ASTM B584 alloy C90500, with dual-seal rubber encapsulated disc and Type 304 stainless steel stems. The rubber encapsulation shall be Gr. “E-pw” EPDM for cold and hot potable water use, UL Classified in accordance with ANSI/NSF61. The valve shall be equipped with a 10-position lever handle.
6.11 Strainers: Grooved-end Y-type strainers for CTS (copper tubing) shall be Shurjoint Model C726, 2” (DN50) through 6” (DBN150), rated 300 psi, consisting of a bronze body per ASTM B584 alloy C90500 and Type 304 perforated screen, assembled with a C305 coupling and C60 cap.
6.12 Dielectric Transition Fitting: Dielectric transition fittings shall be Shurjoint Model DE30-GG for sizes 2” (DN50) through 8” (DN200), which shall provide effective insulation between the IPS and CTS systems to avoid galvanic local cell and stray current problems. The dielectric transition fitting shall be made of ductile iron per ASTM A536 Gr. 65-45-12, electric deposition coated, with a virgin PP (propylene) lining.
Section 7: AWWA Ductile Iron Pipe Grooved Piping Systems
7.1 General: The Shurjoint grooved method can be selected for joining grooved end AWWA ductile iron pipe and fittings in lieu of the spigot & socket method at buyer’s option and may be used in, but not limited to, water, waste water, reclaimed water, and sewage subject to local code approval and installation in accordance with manufacturer’s installation instructions.
7.2 AWWA Ductile Iron Pipe: AWWA ductile iron pipe shall to (add applicable standards).
7.3 Pipe End Preparation: Pipe ends shall be cut-grooved in accordance with the radius cut-groove specifications per AWWA C606, either rigid radius cut groove or flexible radius cut groove depending on the intended service. Pipe ends shall be free from indentations, projections, burrs, roll marks, etc. in the area where gaskets are seated.
7.4 Couplings: Couplings shall be made of ductile iron conforming to ASTM A536 Gr. 65-45-12, painted black.
7.5 Bolts: Carbon steel track bolts shall conform to ASTM A183 Gr. B, minimum tensile strength 110,000 psi, zinc plated to ASTM B633 with carbon steel heavy duty nuts per ASTM A563 Gr. A. For buried service, bolts shall be stainless steel conforming to ASTM A193 Grade B8 (304) or B8M (316).
7.6 Gaskets - Gaskets shall be a pressure responsive design, molded of Grade “S” Nitrile or Grade “M” Halogenated Butyl or Grade “L” Silicone as designated by ASTM D2000.
7.6.1 Grade “M” halogenated butyl gaskets shall be used for water service plus a variety of dilute acids, oil-free air and other chemical services within the temperature range of -20oF(-29oC) to +200oF (+93oC). Grade “M” gaskets are not recommended for petroleum services. Grade “M” gaskets shall be identified with a brown stripe code
7.6.2 Grade “S” Nitrile gaskets shall be used for oil services including petroleum products*, air with oil vapors, vegetable and mineral oils within the temperature range of -20oF (-29oC) to +180oF (+82oC) and air and water under +150oF (+65oC). Grade “S” gaskets are not recommended for hot water services. Grade “S” gaskets shall be identified with a red stripe code. (* Not recommended for services of gasoline, diesel oil, jet fuels and or naphtha.)
7.6.3 Grade “L” silicone gaskets shall be used for dry heat, air without hydrocarbons within the temperature range of -30oF (-34oC) to +350oF (+177oC). Grade “L” gaskets shall be identified by the compound color of red.
7.7 Grooved Couplings:
7.7.1 Grooved couplings shall be Shurjoint Model A505 for AWWA pipe sizes 3” (DN80) through 24” (DN600). The Model A505 coupling shall be used either as a rigid coupling or flexible coupling depending on the grooves processed. The Model A505 coupling shall be supplied painted black with a GapSeal* gasket and the gasket grade shall be selected depending on the service intended. (*The GapSeal gasket is designed to seal the gap between the pipe ends.)
7.7.2 Transition couplings from an IPS grooved system to a grooved AWWA ductile iron pipe system shall be Shurjoint Model A507 transition couplings for pipe sizes 3” (DN80) through 12” (DN300).
7.8 Flange Adapters: Flange Adapters for direct connection from an ANSI Class 125 / Class 150 flanged system to a grooved end AWWA ductile iron pipe shall be Shurjoint Model A512 for pipe sizes 3” (DN50) through 12” (DN300). Model A512 flange adapters shall be made of ductile iron per ASTM A536 Gr. 65-45-12, painted black, with a Grade “M” EPDM gasket and a pair of hexagonal bolts for joining the flange segments. Drillings shall conform to and testing shall be conducted in accordance with ANSI B16.5 Class 150.
7.9 Grooved-end Fittings shall be Shurjoint Model A10 (90° Elbow), A11 (45° Elbow), A12 (22½° Elbow), A13 (11¼° Elbow), A20 (Tee), A60 (Cap), A25 (Reducing Tee), A50 (Concentric Reducer) and A10R (Reducing elbow). Grooved-end fittings shall be made of ductile iron castings conforming to ASTM A536 Gr. 65-45-12 with C-to-E dimensions to ANSI A21.10/AWWA C110 and wall thickness to AWWA C153 or ANSI A21.10 /AWWA C110.
Section 8: HDPE Plain End Piping System
8.1 General: The Shurjoint plain-end piping method can be selected for joining plain end HDPE (high density polyethylene) pipe in lieu of the heat fusion method at buyer’s option and may be used in, but not limited to, water, waste water, hydro transport systems, irrigation, sewer storm & sanitary pipelines subject to local code approval and installation in accordance with manufacturer’s installation instructions.
8.2 HDPE Pipe: HDPE (high density polyethylene) pipe shall conform to ASTM D2447, D3035 or F714 or shall conform to ISO 161/1, AS 1159 and DIN 8074, with wall thickness from SDR 32.5 to 7.3. The Shurjoint HDPE couplings shall not be used for PVC or other plastic pipe.
8.3 Pipe End Preparation: No special pipe end preparation shall be required. Pipe shall be used as supplied from the manufacturer. Pipe ends shall be free from indentations, projections, burrs, roll marks, etc. in the area where gaskets are seated.
8.4 Bolts: Carbon steel track bolts shall conform to ASTM A183 Gr. B, minimum tensile strength 110,000 psi, zinc plated to ASTM B633 with carbon steel heavy duty nuts to ASTM B563 Gr. A.
8.5 Gaskets: Gaskets shall be pressure responsive design, molded of Grade “E” EPDM or Grade “T” Nitrile elastomer as designated in ASTM D2000. The Grade “E” EPDM gasket shall be used for cold and hot water services for temperatures from -30oF (-34oC) to +230oF (+110oC), plus a variety of dilute acids, oil free air and other chemical services as allowed in the manufacturer’s gasket selection guide. The Grade “E” gasket shall not be used for petroleum oils, mineral oils, solvents, aromatic hydrocarbons and steam services. The Grade “T” Nitrile gasket shall be used in a variety of oil services including petroleum products*, vegetable oils, mineral oils, and air with oil vapors for temperatures from -20°F (-29°C) to +180°F (+82°C) and water for temperatures lower than +150°F (+65 °C). For other services, select the correct gasket grade in accordance with the manufacturer’s gasket selection guide. (* Not recommended for services of gasoline, diesel oil, jet fuels and or naphtha.)
8.6 Lubricant: Gaskets shall be lubricated with corn oil, glycerin, silicone oil, or silicone release agent. Do not use Shurjoint lubricant 550H, greases, soap-based solutions, or hydrocarbon based oils.
8.7 Plain-end Couplings:
8.7.1 Plain-end couplings shall be Shurjoint Model H305 IPS sizes 2” through 20” or ISO sizes DN50 through DN315. The Model H305 coupling shall have sharp machined teeth and supplied with a Grade “E” EPDM or Grade “T” Nitrile gasket and four carbon steel track bolts and nuts.
8.7.2 For transition from a grooved end IPS steel pipe system to a plain end HDPE pipe system, use Shurjoint Model H307 transition couplings for IPS pipe sizes 2” through 12” or ISO pipe sizes DN63 through DN200.
8.8 Flange Adapters for direct connection from an ANSI Class 125 / Class 150 flanged system to a plain end HDPE pipe system shall be Shurjoint Model H312 for IPS pipe sizes 4” through 12” or ISO pipe sizes DN110 through DN315. Model H312 flange adapters shall be made of ductile iron per ASTM A536 Gr. 65-45-12, painted orange, with a Grade “E” EPDM gasket and a pair of hexagonal bolts for joining the flange segments. Drillings shall conform to and testing shall be conducted in accordance with ANSI B16.5 Class 150.
Section 9: IPS Steel Plain End Piping Systems
9.1 General: The Shurjoint plain-end piping method can be selected for joining plain end or beveled end carbon steel pipe in lieu of the flanged, welded, grooved, or threaded method at buyer’s option. IPS steel pipe plain end piping method may be used in, but not limited to, repairs and maintenance including roof drains, slurries, tailings and oil field services subject to local code approval and installation in accordance with manufacturer’s installation instructions.
9.2 Carbon Steel and Stainless Steel Pipe: Carbon steel and stainless steel pipe shall be of IPS sizes with hardness less than HB 150.
9.3 Pipe End Preparation: No special pipe end preparation shall be required. Pipe shall be used as supplied from the manufacturer. Pipe ends shall be free from indentations, projections, burrs, roll marks, etc. in the area where gaskets are seated.
9.4 Bolts: Carbon steel track bolts shall conform to ASTM A183 Gr. B, minimum tensile strength 110,000 psi, zinc plated to ASTM B633 with carbon steel heavy duty nuts to ASTM A563 Gr. A.
9.5 Gaskets - Gaskets shall be pressure responsive design, molded of Grade “E” EPDM or Grade “T” Nitrile elastomer as designated in ASTM D2000. The Grade “E” EPDM gasket shall be used for cold and hot water services for temperatures from -30oF (-34oC) to +230oF (+110oC), plus a variety of dilute acids, oil free air and other chemical services as allowed in the manufacturer’s gasket selection guide. The Grade “E” gasket shall not be used for petroleum oils, mineral oils, solvents, aromatic hydrocarbons and steam services. The Grade “T” Nitrile gasket shall be used in a variety of oil services including petroleum products*, vegetable oils, mineral oils, and air with oil vapors for temperatures from -20°F (-29°C) to +180°F (+82°C) and water for temperatures lower than +150°F (+65 °C). For other services, select the correct gasket grade in accordance with the manufacturer’s gasket selection guide. (* Not recommended for services of gasoline, diesel oil, jet fuels and or naphtha.)
9.6 Plain-end Couplings: Plain-end couplings for IPS steel pipe shall be Shurjoint Model 79, consisting of ductile
iron housings per ASTM A536 Gr. 65-45-12, case-hardened carbon steel jaws*, a Grade “E” EPDM or Grade “T” Nitrile gasket and carbon steel track bolts and nuts. Shurjoint Model 79 couplings shall not be used on HDP, cast iron or other brittle pipe. (*Jaws shall be made of 17-4PH stainless steel for larger sizes than 14” (DN350)).
Section 10: CPVC Grooved Piping System
10.1 General: The Shurjoint grooved piping methods can be selected for joining CPVC pipe in lieu of the solvent cement method at buyer’s option. Shurjoint CPVC grooved piping method may be used in, but not limited to, plumbing, water distribution systems including potable water, and fire protection systems subject to local code approval and installation in accordance with manufacturer’s installation instructions.
10.2 CPVC Pipe: CPVC pipe shall conform to ASTM F441 – CPVC Schedule 80 and or ASTM F442 – CPVC IPS SDR 13.5. Acceptable tradenames of CPVC pipe are the FlowGuard Gold®, BlazeMaster® and Corzan® (FGG/BM/CZ™). Applicable sizes shall be 2” (DN50) through 8” (DN200). All CPVC fire sprinkler pipe shall be UL listed for wet pipe systems and shall carry a rated working pressure of 175 psi @150°F (1.23 MPa @65°C).
10.3 Pipe End Preparation: CPVC pipe shall be cut-grooved to AWWA C606. Roll-grooving is not acceptable. Pipe shall be used as supplied from the manufacturer. Pipe ends shall be free from indentations, projections, burrs, roll marks, etc. in the area where gaskets are seated.
10.4 Gaskets: Gaskets shall be a pressure responsive design, molded of Grade “E” EPDM, designation 2CA615A25B24F17Z per AWWA C606. The Grade E gasket shall be used for cold and hot water services for temperatures up to +180oF (+82oC), plus a variety of dilute acids, oil free air and many chemical services. Grade “E” gaskets are not recommended for petroleum oils, mineral oils, solvents, aromatic hydrocarbons and steam services. Grade “E” gaskets shall be identified with a green color code. Gasket materials used for potable water systems shall be in compliance with NSF 61.
10.5 Bolts: Carbon steel track bolts shall conform to ASTM A183 Gr. B, minimum tensile strength 110,000 psi, zinc plated to ASTM B633 with carbon steel heavy duty nuts to ASTM B563 Gr. A.
10.6 Grooved Coupling: The grooved coupling for use with CPVC pipe shall be Shurjoint Model 7705 and Model 7707 flexible couplings. Housings shall be made of ductile iron per ASTM A536 Gr. 65-45-12. Acceptable grooved couplings for use with CPVC pipe shall be identified with a tag showing “FGG/BM/CZ™ System Compatible”. Rigid type couplings shall not be used for CPVC piping.
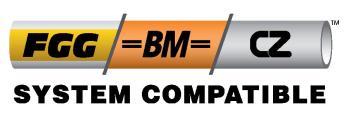
FlowGuard Gold®, BlazeMaster® and Corzan® are registered trademarks of Lubrizol Advanced Materials Inc.
Section 11: PVC Grooved Piping System
11.1 General: The Shurjoint grooved piping methods can be selected for joining PVC pipe in lieu of the solvent cement method at buyer’s option. Shurjoint PVC grooved piping method may be used in, but not limited to, plumbing, and water distribution systems including potable water subject to local code approval and installation in accordance with manufacturer’s installation instructions.
11.2 PVC Pipe: PVC pipe shall conform to ASTM D1785 – PVC Schedules 40 and 80 and or ASTM D2241 – PVC IPS SDR-PR. Applicable sizes shall be 2” (DN50) through 8” (DN200).
11.3 Pipe End Preparation: PVC pipe shall be roll-grooved to AWWA C606. Pipe ends shall be free from indentations, projections, burrs, roll marks, etc. in the area where gaskets are seated.
11.4 Gaskets: Gaskets shall be a pressure responsive design, molded of Grade “E” EPDM, designation 2CA615A25B24F17Z per AWWA C606. The Grade E gasket shall be used for cold and hot water services for temperatures up to +180oF (+82oC), plus a variety of dilute acids, oil free air and many chemical services. Grade “E” gaskets are not recommended for petroleum oils, mineral oils, solvents, aromatic hydrocarbons and steam services. Grade “E” gaskets shall be identified with a green color code. Gasket materials used for potable water systems shall be in compliance with NSF 61.
11.5 Bolts: Carbon steel track bolts shall conform to ASTM A183 Gr. B, minimum tensile strength 110,000 psi, zinc plated to ASTM B633 with carbon steel heavy duty nuts to ASTM B563 Gr. A.
11.6 Grooved Coupling: The grooved coupling for use with PVC pipe shall be Shurjoint Model 7705 and Model 7707 flexible couplings, Model 7706 reducing coupling, XH-1000 rigid coupling, and Model C-7 outlet coupling, Housings shall be made of ductile iron per ASTM A536 Gr. 65-45-12.