PIPE END PREPARATION
How to process roll-grooves
Shurjoint grooved piping systems require the processing of a roll or cut groove to the pipe ends being connected. The engagement of the housing keys in the grooves is integral in providing a secure and leak-tight joint. It is essential that the grooves are properly processed for optimum joint performance.
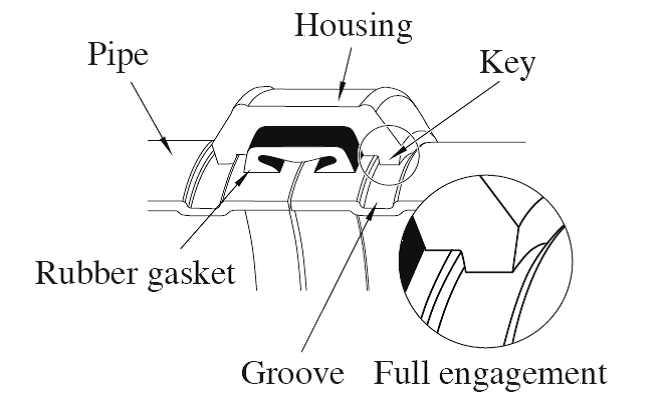
Nominal pipe size
Shurjoint couplings and fittings are identified by the nominal IPS pipe size in inches or nominal diameter of pipe (DN) in millimeters. Always check the actual O.D. of the pipe and fittings to be connected, as in some markets it is customary to refer to different O.D. pipes with the same nominal size.
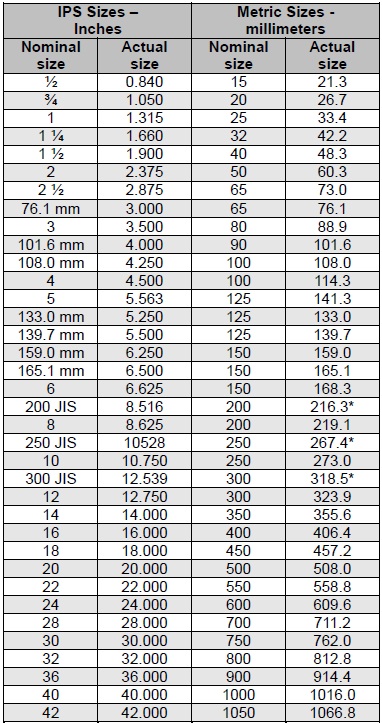
*JIS/KS
Roll groove standard
Roll grooves must meet the specifications and requirements of ANSI/AWWA C-606-04 Table 5. For other pipe sizes not specified in this standard, refer to the applicable groove specifications shown in this catalog or Shurjoint installation manual.
Square cut
Pipe ends must be square cut. Always use a pipe band-saw or automatic round-saw for cutting pipe. The maximum allowable tolerances from square ends are .03"/0.8mm for sizes up to 3½"/ 90 mm; 0.045"/1.2 mm for 4" thru 6"/100 mm thru 150 mm and 0.060"/1.6 mm for sizes 8"/200 mm and above.
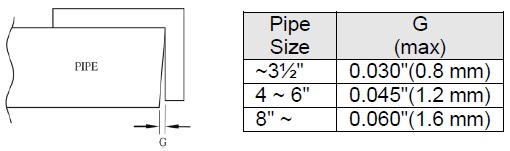
Applicable pipe wall thickness
Roll grooves are generally applicable to 0.375"/ 9.5 mm thick or thinner wall carbon steel pipe, stainless steel pipe, copper tube and aluminum pipe depending on the type of roll-grooving machine and roll set being used. Different wall thicknesses and sizes require the use of different roll sets as with Sch. 10 and Sch. 40 pipe as shown.
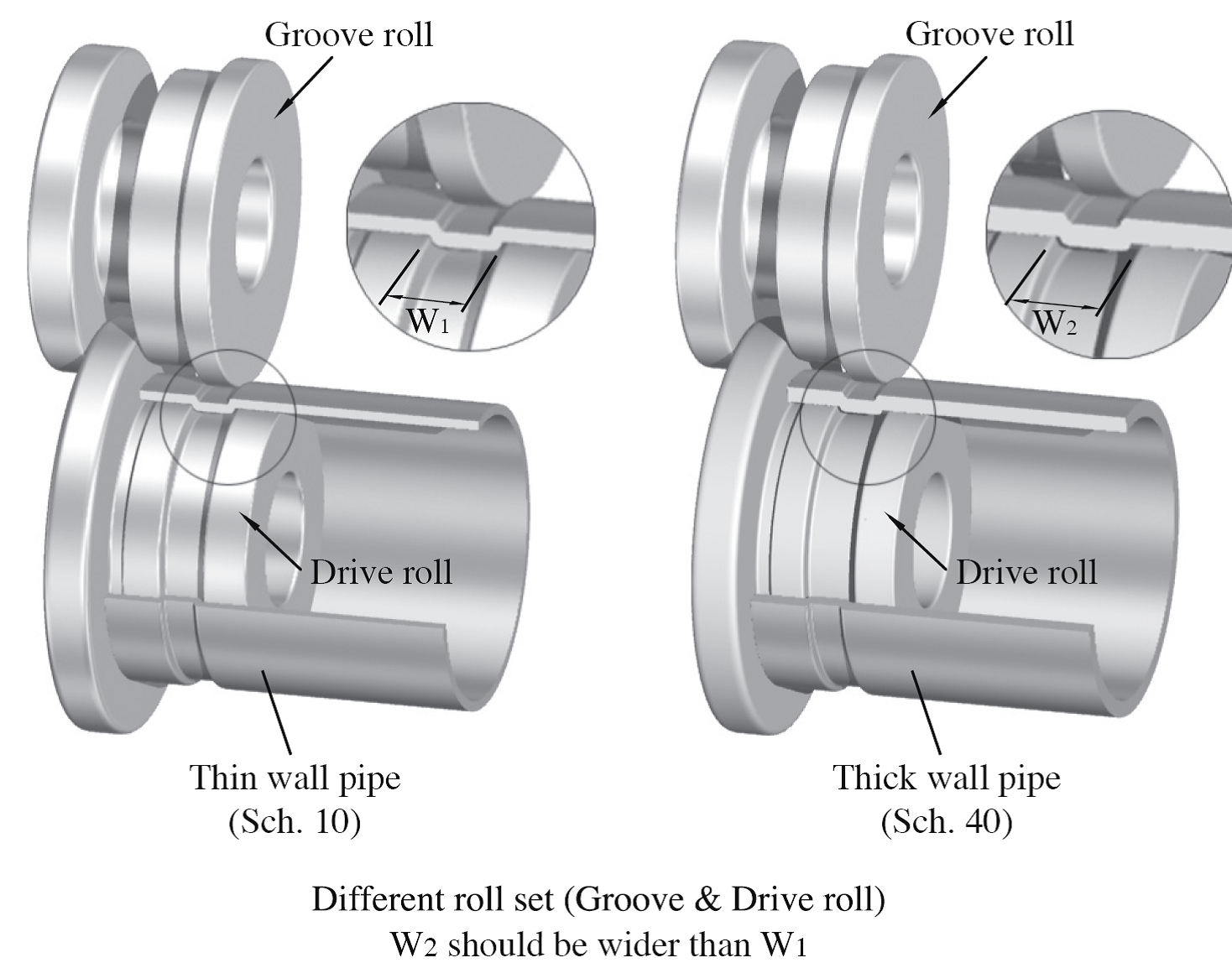
Plain end pipe and beveled end pipe
While plain-end pipe is preferred, the use of beveled end pipe is acceptable providing that the wall thickness is 0.375"/9.5 mm or thinner and the bevel is 37½±2½° or 30° as specified in ANSI B16.25 and ASTM A-53 respectively.
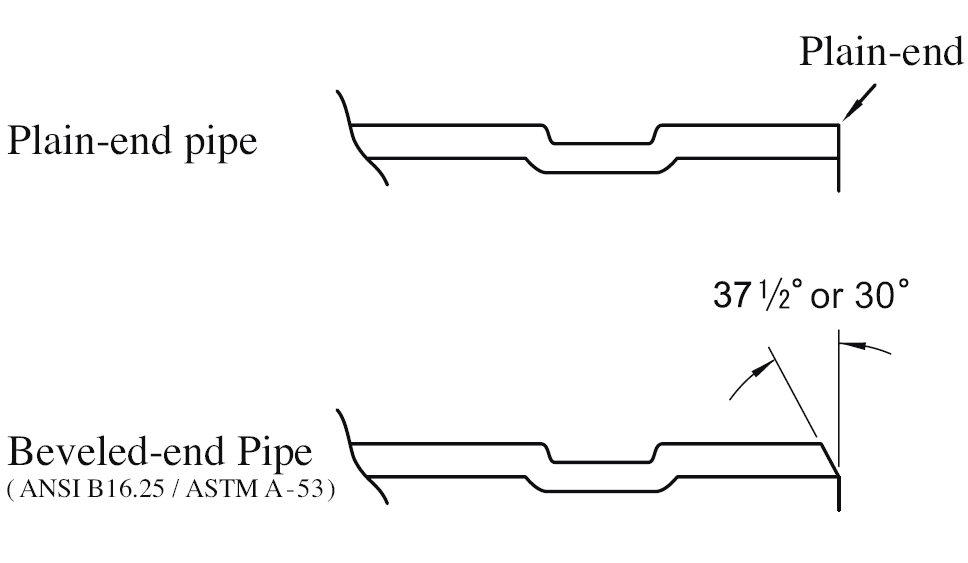
Galvanized pipe
Galvanized pipe is acceptable as long as the gasket seating surface is smooth and free from scale and imperfections that could affect gasket sealing. Whenever you remove welding beads or projections from the sealing surface of galvanized pipe, use caution so as to not overgrind the surface. After grinding, always apply a proper rust prevention coating to this area.
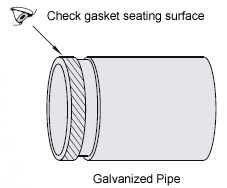
Heavy wall pipe
When you attempt to roll-groove pipe thicker than 0.375"/9.5 mm, the metal may deform and heap up on both sides of the groove rather than radially deforming and protruding on the inside of the pipe. The extra heaped metal on the sealing surface may preclude the coupling housings from making metal-to-metal contact, which could lead to joint failure. In such a case, you should grind off any such extra metal to achieve a flat and smooth sealing surface. A proper rust preventative coating must be applied on the ground surface. Shurjoint strongly recommends the processing of cut-grooves on heavy or thick wall pipe.
.jpg)
Weld Beads
ERW pipe is one of the most popular types of pipe used today. Depending on the individual pipe and manufacturer, welding beads may remain on the surface (inside and out) of the pipe. Always remove harmful weld beads near the pipe ends as they can cause rattling of the roll grooving machine resulting in inaccurate grooves.
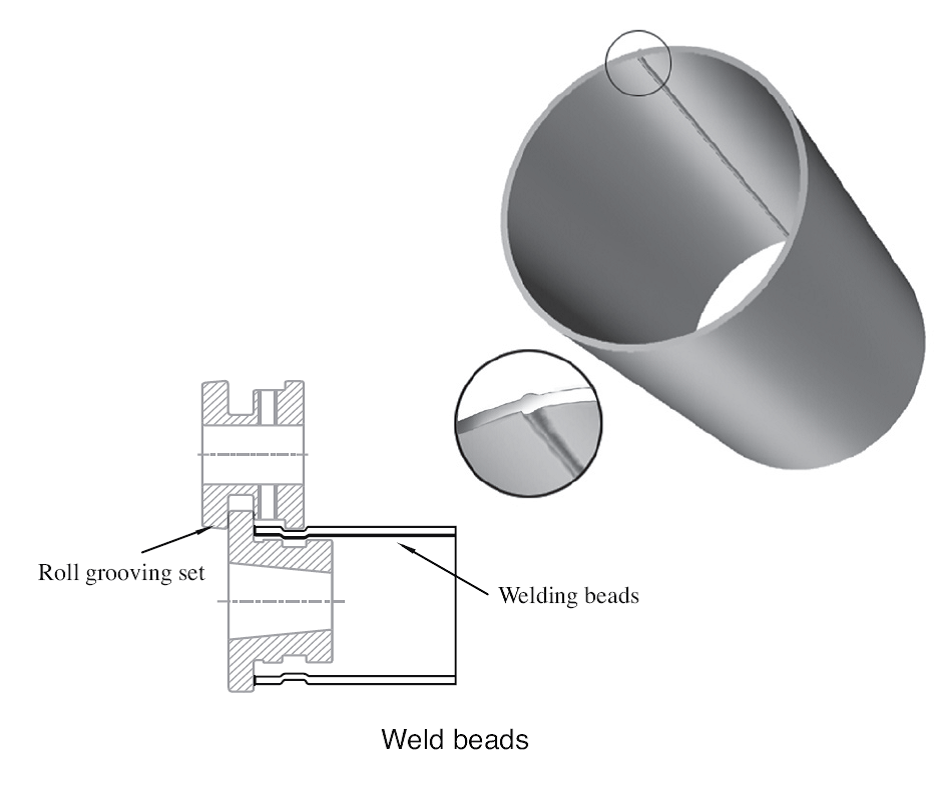
Spiral welded pipe
Spiral welded pipe may be used as long as the weld beads are removed from the gasket seating surface. It is also acceptable and recommended to weld a grooved end nipple to the pipe end as shown below. Whenever you remove weld beads or projections from the gasket seating surface, use caution so as to not over-grind the surface. After grinding, always apply a proper rust-prevention coating to this area.
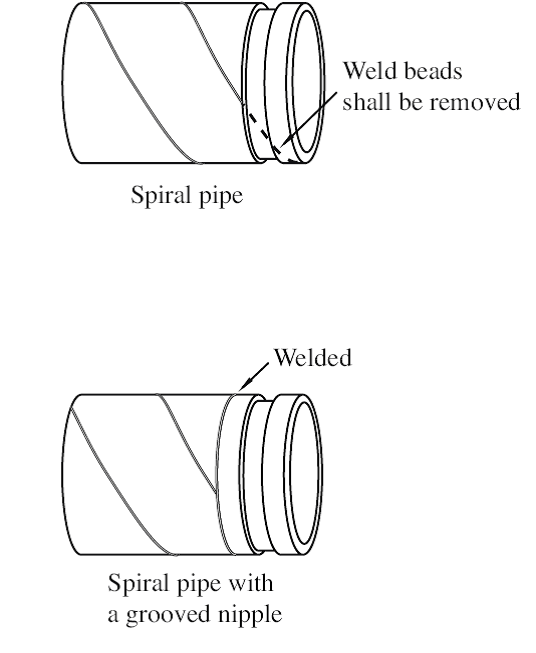
Stainless steel pipe
Stainless steel pipe in general is more difficult to groove than carbon steel pipe, as it is more difficult to achieve defined groove corners on stainless pipe. Grooves that are not defined and have too much of a radius could result in joint failure. Care must be taken to process grooves as defined as possible. For this reason, roll-groove machine manufacturers offer a variety of roll sets depending on the pipe material and wall thickness being grooved. Always select the correct roll set for the pipe being grooved.
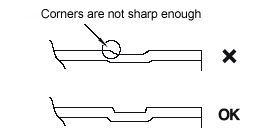
Caution: If the same roll-set that has been used for carbon steel pipe is used on stainless steel pipe, rust or scale may be transferred to the stainless steel pipe during processing of the groove. Thus we recommend the use of a separate roll set specifically for use with stainless steel pipe. Also use caution to keep roll grooved stainless steel pipe dry prior to installation.
PVC pipe
The same roll set used for carbon steel pipe can be used on applicable PVC pipe. Because PVC is much softer than carbon steel, care must be taken to groove the pipe slowly and with less pressure.
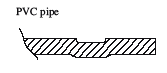
Copper tubing
As copper tubing is thinner than carbon steel pipe, always use a roll set specifically designed for use on copper tubing.
Gasket seating surface (A)
The exterior surface of the gasket seating area shall be free from any indentations, projections, roll marks or other harmful defects such as loose paint, scale, dirt, chips, grease and rust.
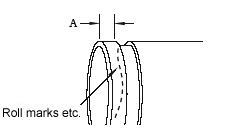
Roll groove profile
Roll grooves should be as defined as possible. To achieve optimum joint performance the "K" dimension should be as small as possible. When processing a roll groove the machine operator should manage the feed pressure of the upper roll set so as to achieve the best possible groove profile.
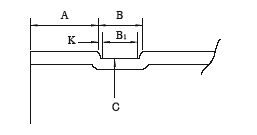
Groove diameter (C)
The groove diameters are average values. The groove must be of uniform depth around the entire pipe circumference. Use a Shurjoint groove gage or groove measuring tape to check the groove diameter.
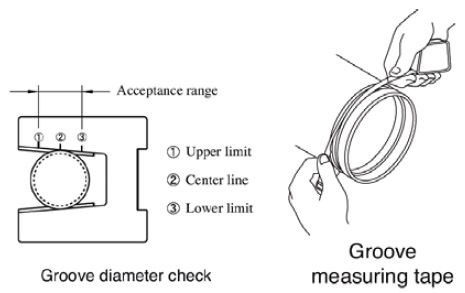
Or you can use a coupling housing for a quick check after verification of the groove dimensions. When using a housing segment as a reference always make up a sample and verify the diameter is within the acceptable range. If the housing fits well you may choose to use this as a reference gauge.
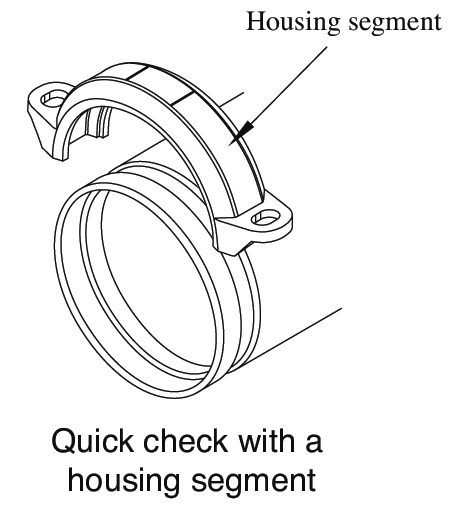